A FDM 3D printer runs on either a direct drive or a Bowden extrusion system. And as a user of FDM 3D printer, sooner or later you'll face the question, direct drive extruder or Bowden extruder, which to choose. Now let's start from the basics of 3D printing extrusion, and get to know the pros and cons of direct drive and Bowden extruders, and learn to decide which to choose for your specific 3D printing jobs.
What is Extrusion in 3D Printing?
Extrusion in 3D printing is the process of a material being pushed into the melt zone, heated and deformed to flow out of a nozzle. It's more commonly known as Fused Deposition Modeling (FDM) or Fused Filament Fabrication (FFF).
What is a Direct Drive Extruder?
In a direct drive system, the extruder is mounted just over the top of the hotend. This means the extruder pushes filament directly into the hotend without any additional components in between.
Pros & cons of direct drive extruder
Of course, the way that a direct drive extruder is mounted and works, does really bring us a lot of helpful features. But meanwhile, we also see some downsides on it.
Pros:
1. Better and more reliable extrusion
Since a direct drive extruder is mounted just above the hotend, the motor can directly push the filament into the melt zone and then throughout the nozzle. A direct drive extruder provides better and more reliable extrusion.
2. Easier and faster retraction
Due to the shorter distance between the extruder and the nozzle, a direct drive extruder retracts filament much easier and faster.
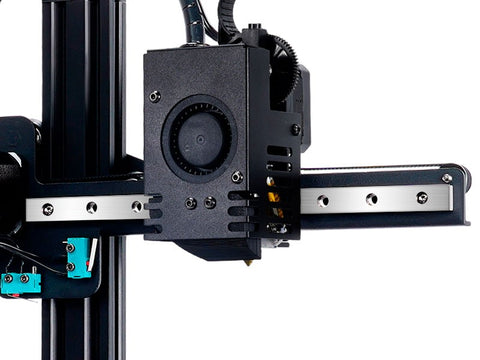
3. Smaller motor also works
Less distance to push in the filament, a direct drive extruder requires less power to work. Hence, smaller motor with less torque also works on a direct drive extruder.
4. Suitable for a wider filament range
A direct drive extruder has a wider compatibility with different filament material. It works well with not only commonly used PLA, but also flexible filaments like TPU, TEPG and abrasive filaments like nylon.
Cons:
1. More vibration
Mounted directly onto the hotbed, a direct drive extruder obviously adds a lot of weight to the print head. Hence the print head moves with possibly more vibration and speed limitation. Wobble happens more and leads to a certain loss of X and Y-axis accuracy.
2. Difficult to maintain
Since the direct drive extruder is mounted on top, we have less access to the lower components and maintenance for the hotend becomes more difficult. For example, to clean the nozzle, we have much more complex procedures to go.
What is a Bowden extruder?
Unlike a direct drive extruder, a Bowden extruder is always mounted on the frame of the printer and moves along the Z-axis lead screw. It connects to the hotend with a Bowden tube (also known as teflon tube or PTFE tube).
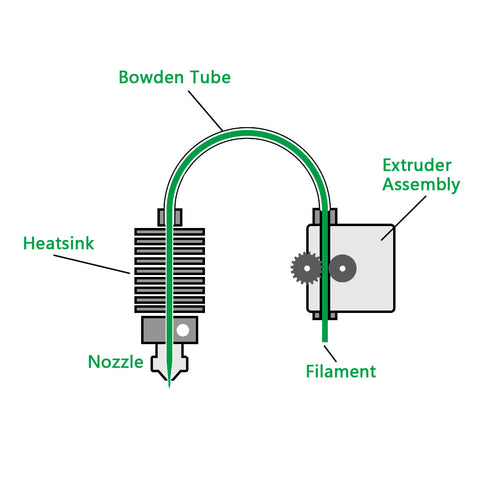
Pros and cons of Bowden Extruder
The construction of a Bowden extruder means a longer distance between the extruder and the hotend but less weight on the print head. Hence we also see both pros and cons on a Bowden extruder.
Pros:
1. Less weight on the print head
It's easy to get the idea that a lighter print head on a Bowden 3D printer moves along the X-axis with less vibration, cleaner movement and increased speed than on a direct drive 3D printer. Thus, we get increased printing speed and better accuracy on X and Y-axis.
2. Possible larger build volume
Less size of the print head on a Bowden 3D printer often means possible larger build volume when comparing with a direct drive 3D printer in almost the same frame size and design. It's simply because smaller print head has more space to move up and down.
Cons:
1. Requires more powerful motor
More powerful motor with high torque is required to push the filament through the long PTFE tube into hotend for a Bowden extruder.
2. Much longer response time
The long PTFE tube also increases the friction when pushing the filament inside. It produces a noticeable delay of response time, which means longer but faster retraction is needed to avoid tension.
3. Less filament compatibility
The longer distance to travel inside the PTFE tube of a Bowden extruder leads to possible filament coil or even clog, especially on either flexible or abrasive filaments like TPU, TEPG, nylon, and etc. Hence, we get filament limitations when print on a Bowden 3D printer. Insisting to print certain kinds of filament on a Bowden 3D printer, you have to overcome a lot of difficulties and issues to succeed.
Conclusion
After going through all the above contents, including the features, and pros and cons of the direct drive extruder and the Bowden extruder, finally we come to the ending.
It's not difficult to conclude the biggest differences between a direct drive extruder and a Bowden extruder into two elements, the distances to travel for the filament and the weights of their print heads.
With less distance for the filament to travel inside a direct drive extrusion system, a direct drive 3D printer has much wider filament compatibility and is more recommended for printing flexible materials like TPU.
With less weight and more stability on the print head, a Bowden 3D printer is more preferred for higher printing speed and relatively a little bit higher accuracy on X and Y-axis if you don't print flexible filament.
My belt came apart how do I fix it